Interview with Tomáš Vondrák: Hope in steel
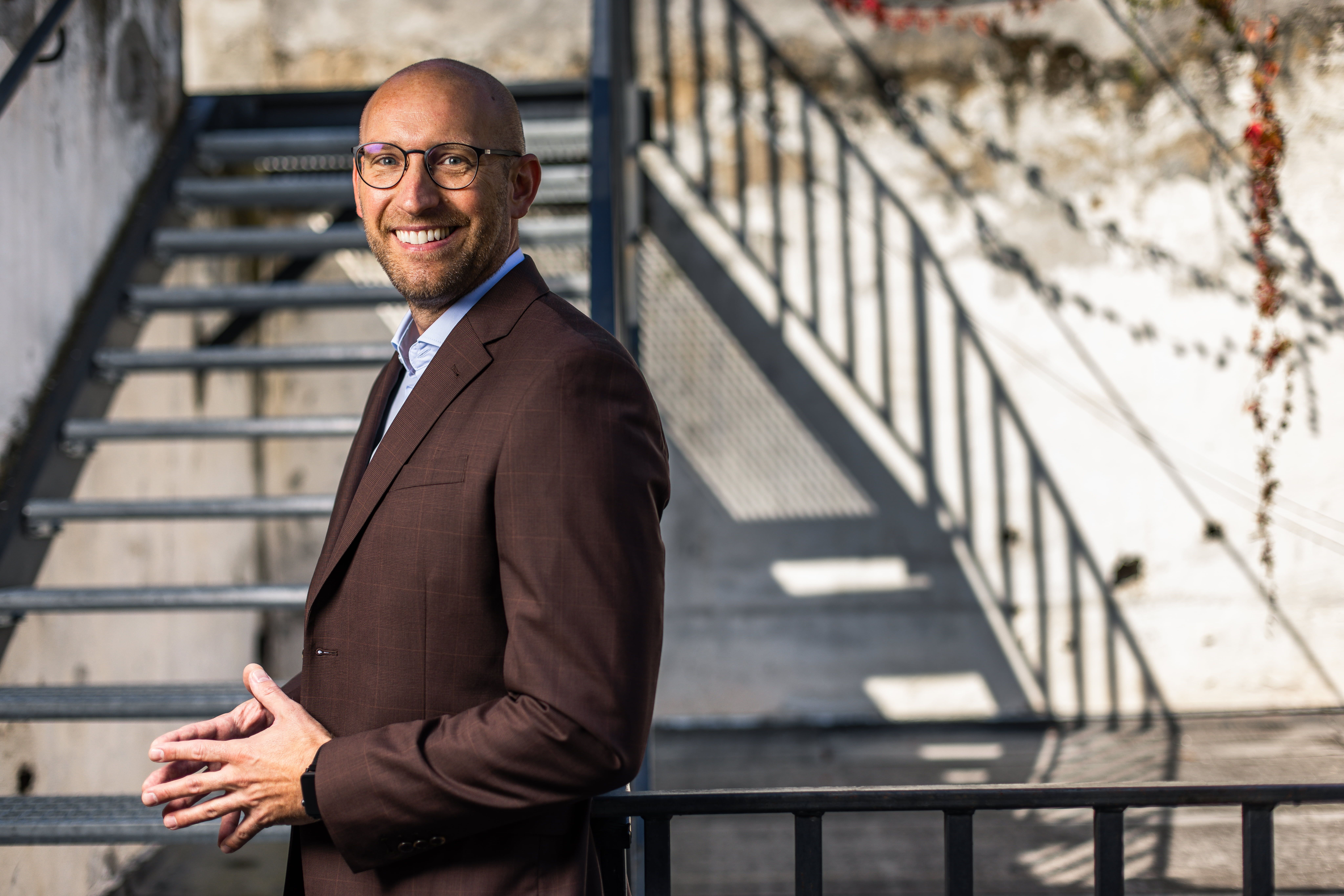
He is a revelation on the construction market. After all, the ambitions of the startup Auklan are not small – thanks to the construction of residential properties made of steel on an industrial scale, it wants to lead the Czech Republic out of the protracted housing crisis. “Instead of the three years it usually takes to build a house, we are able to produce it in two production shifts. And save investors a tenth of the cost,” says Tomáš Vondrák, a member of Auklan’s board of directors and director of NB Holding, under which the company falls.
What does the "industrialisation of residential construction" mean in your concept, as you publicly refer to it?
We are responding to the current situation on the domestic real estate market, where there is currently a shortage of 50 to 100 thousand flats, primarily in Prague, according to various calculations. The logic behind the industrialisation is the fact that we produce complete 2D steel walls in the industrial conditions of our engineering production. The NB Holding Group is a group of five companies, including 1SCS and Mars, which have many years of experience in steel processing and engineering production, for example for the automotive sector. For the entire group, we process around 70,000 tonnes of steel per year. As a result, we at the startup Auklan are able to "produce construction" 12 months a year regardless of the weather, in addition to the automation of production in millimetre precision engineering. This is, dare I say, a truly unparalleled advantage compared to the normal reality on construction sites.
How many flats can you "produce", to give you an idea?
This year, we are able to supply the market with from 500 housing units, where by housing unit we mean an apartment of 65 square meters. Next year already a thousand and in two and a half to three years from two and a half thousand housing units. Our motivation is to make housing in the Czech Republic affordable again. This mission makes a lot of sense to us.
Where did this idea come from?
The owner of the holding is a great visionary and thinks about what technologies to apply in different market segments. Thin-walled steel construction, or LGSF (light gauge steel frame), is widespread in the USA, New Zealand and Europe, for example. It has a firm place in the UK or the Netherlands, where the market has started to have a larger capacity of housing units thanks to sophisticated construction, and over the last decade the average price of apartments, or rental costs, has decreased as a result.

Are you saying, in practical terms, that LGSF technology has eliminated the housing shortage in local markets?
It is one of the important factors. It has improved the housing situation, after all, in cities like Amsterdam, the apartments that are available today are cheaper than in Prague. There are many advantages to building with thin-walled steel. The profiles made from it are light on the one hand and rigid and strong on the other, which are excellent prerequisites for building stability. As far as the composition of the 2D walls is concerned, we design them to a low-energy to passive standard, which reduces the energy costs per housing unit by 50 to 75 percent. At the same time, the technology has a great added value for owners and tenants in terms of layout - the thinness of the walls increases the usable area.
How much can you increase the usable area compared to a brick or concrete house?
Standardisation and modularity allows, for example, in the apartment building projects we are developing, to achieve a very high net floor area ratio for usable housing of 80 per cent through good distribution of units. This is a really good result, and definitely interesting for investors. However, we have to take into account the fact that we are trying to design the building so that all the walls are load-bearing. This means that we do not expect any walls to be left out or rebuilt in the future. There is a certain limitation, but if the project takes this into account, such an intervention is very easy to implement even years later.
What about the acoustics, for example, is it not audible to the neighbours because of the thinness of the walls?
We regularly get questions about acoustic resistance and the general user quality of housing. I have looked at several reference buildings abroad and I have to confirm that the user quality is very high. Whether it is an apartment or a house, the client has no way of knowing if it is an LGSF construction or a standard brick construction. On the contrary, in some cases, the acoustics were at a better level than in standard technology construction.

If the construction of thin-walled steel is full of advantages, as you describe, why hasn't it reached the Czech market yet?
I see the Czech construction industry as relatively conservative. We all know how many years wooden buildings have been trying and trying to establish themselves on the market to a greater extent, and yet last year only around 14 percent of new construction was made of wood.
In other words, acceptance of technological change is lower in the domestic construction market, even though there is a real housing shortage. We seem to have a strongly ingrained sense of ownership, especially for custom housing, where the investment is tied to the value element of brick.
One of the main reasons why it is not being built, however, lies in the area of legislation and lengthy procedural procedures.
Undoubtedly, the legislative process of building permits takes a long time in the Czech Republic, and we all hope that the new Building Act and the digitalisation of the building procedure will speed it up. However, we believe that the sooner we are involved in a given project, perhaps with a developer or investor from the stage of a zoning change and a binding planning or design study, the more we can speed up the whole process and ultimately on the permitting side.
So how long does it take you to build a house?
For comparison, last year about 40,000 housing units were built, 40 percent of which were in apartment buildings, with the average construction time for an apartment or single-family home being between 33 and 40 months. For us, it is lower units of months. Yet speed is one of the key aspects of financing. As an investor, do you put money into a project that you can only sell in four years, or do you put it in 6 to 9 months, 70 per cent faster? Or imagine that, in the case of a municipal project, you will be able to offer the target group, be it health professionals, teachers or police officers, rental capacity two to three years earlier.
Do you design standard buildings and then produce them virtually in series, or do you make each house to measure?
In terms of product segmentation, our portfolio includes both apartment and family houses, whether individual or terraced. It turns out that the concepts of repeating, identical row houses in terms of design are very effective. Another interesting product are extensions to apartment buildings, which can be realised in a few days. This is ideal if there is a need to increase the capacity of schools, nurseries, senior homes or other social facilities in communities where there is strong demand. We have also designed sports cabins for municipalities, as well as schools and nurseries, which we are able to build within two months of the summer holidays. Tiny houses or small houses of 40 to 60 square meters are also an effective solution. We are also able to offer derivative products such as photovoltaic walls, both for industrial and residential buildings, or carports, i.e. car roofs with photovoltaic panels.

How would steel look in a luxury villa, does one know that metal surrounds the home?
I'm sure he wouldn't. Recently I had a lot of discussions in Slovakia about user comfort in expensive projects for very demanding clients. And they are very satisfied with the utility value and features of the building. A lot of these clients even say that they wouldn't build anything else because it's fast, it's high quality and it's great to live in. And that's the defining factor for her.
Another icing on the cake is that, thanks to the digital twin principle, we're able to bring clients from the comfort of their office via virtual reality directly into our production facility to see how their dream home is made.
How far can clients go in their dreams, how much variability do you offer them?
A lot, of course. From the factory we deliver either a finished 3D construction of the building or 2D panels, which are then used to build the 3D construction on site. Only then does the cladding take place, either with prefabricated building elements and materials or with the chosen alternative. The cladding or external structure of the façade can be wood, cembrit-cerbonite or perhaps sheet metal.
Is a steel house cheaper than a conventional building?
It is individual. However, if we do an average search of the bids we do for larger projects, we can see that we are able to save the investor an average of ten percent compared to competing technologies over the entire project and its financing. This is because we deliver complete 2D panels to a site where, for example, tens of millions of crowns worth of scaffolding does not stand for two years.
How many projects have you already completed in the Czech Republic?
Auklan has been operating for less than two years, we still see it as a startup that is part of an established group. We have already completed our first smaller projects in the Czech Republic and abroad, but we are working with developer-type clients to prepare or bid for larger residential projects. And I hope that we will be able to bring them to the stage of realization, and thus also convince our target groups to choose this technology. Whether it's developers, general contractors or mayors of municipalities
Estate magazine, text by Andrea Votrubová
Auklan gives people the courage to build
Další články
-
Articles
Telescopic constructions for PV: Reliability, availability, efficiency
Read more -
Articles
Thin-walled steel structures and their production: why are they a great advantage for the future of the Czech construction industry?
Read more -
Articles
Steel the future with LGSF constructions
Read more
The first step
is up to you
We will help you with everything else.
-
low cost
-
fast construction
-
sustainability
-
fast return of investment
-
precise quality
AUKLAN a. s.
Vlastimila Pecha 1276/5
627 00 Brno-Černovice
IČ: 14287854 DIČ: CZ14287854
Společnost je zapsána v obchodním rejstříku, vedeném
u Krajského soudu v Brně, oddíl B, vložka 8680